Batching Concrete/ Block Plants and Asphalt Plants
Paddle and Pan MixersSafety procedures must be followed when operating or maintaining a paddle or pan mixer. The operator and maintenance staff should check for damage, malfunctions, or excessive wear to the equipment, as well as irregular occurrences, noises, or odours and should not operate the paddle or pan mixer if any damage or irregularities are detected. All pre-operation checks and inspections should be performed before start-up of the mixer. Shut down, lockout, and tag all machine controls before performing any maintenance, clean-up or blockage clearance operations. | 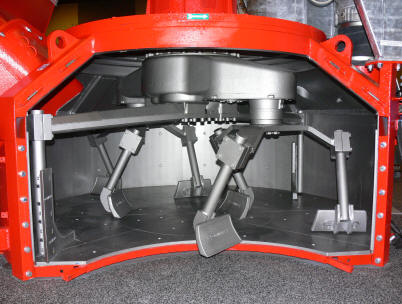 |
The mixer should have interlocks installed at all inspection and maintenance hatches and they must be checked and maintained as part of any maintenance and inspection procedures. If interlocks have been damaged or defeated this is a clear indication that safe procedures are not being followed and should be investigated. Mixers should not be operated when interlocks have been identified as defective/defeated. |
Block PlantsBlock plants have the same conveyor and mixing hazards as other processing operations associated with the quarry industry but they have two added hazards as the concrete is pressed into shape and this presents a risks to persons from the operation of hydraulic rams and during maintenance operations when there are risks during the changing of the mould from falling objects and from operation of the equipment during access. Mobile and fixed equipment should be adequately interlocked when maintenance and mould changing operations take place and manufacturer’s instructions should be followed during mould changing to prevent risks from falling objects. | 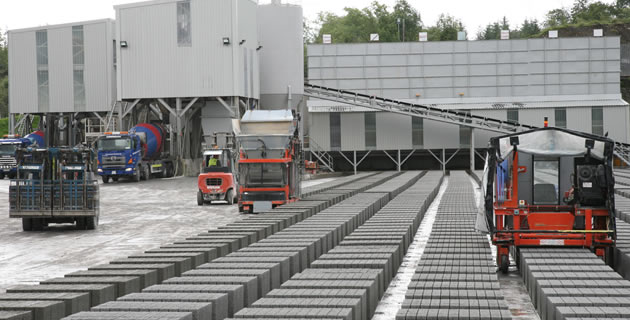 |
Fixed and Mobile block plants also have a high volume of forklift and vehicle operation, often in a small working area and traffic rules optimising pedestrian safety should be prepared. |
Asphalt PlantsAsphalt plants can be very dangerous places. Accidents, sometimes fatal, happen far too often. Most can be traced to the same root cause: the need for production superseding common sense and normal safety practices. Any maintenance procedures on Asphalt plants should follow documented procedures and a lock out/isolation procedure. Inadvertent start -up of plant during maintenance operations has resulted in fatal accidents. Gates with interlocks must be prevented from being closed when persons are inside the restricted area – interlocks must be maintained and checked for safe operation regularly. | 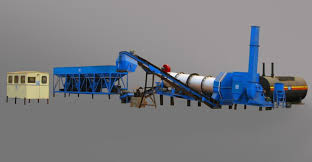 |
Access to skips, vertical and inclined ropeways, conveyors and hoppers should be prevented by adequate guarding and prevention of access to danger areas. Any access gates or doors to these areas should be adequately signposted and be interlocked so that the plant cannot be operated. Maintenance operations must be planned and organised and plant should be isolated and permit to work schemes in operation where necessary. Isolation must not be optional – it is the ‘just a minute’ jobs that lead to the most serious accidents. There are obvious dangers with hot work and with spillages of bitumen but they are not included in this section which focuses on dangers from entanglement with or being struck by process equipment within the plant. Good housekeeping, prevention of spillage, separation of flammable sources from bitumen tanks, good training of staff in deployment of emergency procedures and adequate firefighting equipment are all pre-requisites |