Workshop Safety
An efficient workshop can be one of the most cost-effective ways of maintaining plant and equipment on site. It can also be an area of great risk. The Aggregates & Recycling Information Network (http://www.agg-net.com/) have produced a very detailed workshop inspection checklist for employers that can be tailored to each location to ensure that workshops are operated safely. The number of potential hazards in a workshop will vary on the size and complexity of activities carried out however there are a number of general issues that should be continuously monitored | 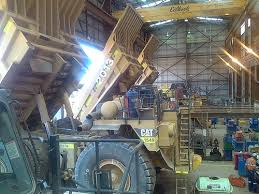
|
Workshops should:
- be well lit;
- be adequately ventilated and where necessary have local exhaust ventilation;
- have a good standard of housekeeping;
- be provided with adequate fire-fighting equipment;
- only contain flammable material necessary for the day to day operation of the workshop;
- only have portable tools that normally operate at 110 volts;
- have clearly identified pedestrian routes and, where possible, reversing of mobile plant should be avoided;
- have pits that are covered when not in use or have guard rails in place;
- have an inspection scheme for all tools and equipment so that they are safe to use;
- have access to workstations restricted to maintenance personnel;
- have gas bottles racked and gas welding bottles should be fitted with a flashback arrestor;
- control the use of naked flames;
- have adequate sanitary and hygienic washing facilities;
- have procedures for waste management of used oils, tyres, batteries, brake and clutch linings etc.