Risk Assessment of Welding
The welding risk assessment must take account of the type of welding, the material being welded, the welding gas used and the electrode or welding rod, in addition to the location, other welding activities, ventilation and the work practices of the welder. Under the Chemical Agents Regulations, the risk must be assessed on the basis of the risk presented by all such chemical agents in combination. These include (not limited to) chromium (VI), nickel, manganese, ozone, Nitrogen oxides, carbon monoxide and chemicals generated by coatings etc. if present.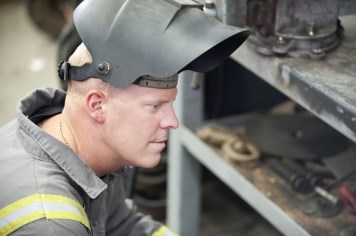
Your risk assessment should also address:
- Noise (this can be different at each ear depending on the position of the welder to the weld)
- Electrical safety
- Fire safety for example, is there a requirement for a hot work permit? What were the previous contents of the item being cut or welded? See Safety Alert - Hot Work on Drums and Containers
- Confined spaces for example, air fed respiratory protective equipment will likely be required
- Weld cleaning for example, specific precautions are required for use of pickling paste (refer to the Safety Data Sheet)
- Welding position
- Optical radiation, for example, ultra violet or infra red light
- Vibration and high speed particles, usually from grinding associated with welding
Where welding is part of your work activity, you must carry out a risk assessment to identify what measures are required to control the risks from exposure to welding fume. This must include the welder and any other workers in the area.
What Controls are Required for Welding Fume?
Follow the guidance in “SLIC Guidance for National Labour Inspectors on addressing health risks from Welding Fume” to reduce the need for welding and to reduce the generation of welding fume for example,
- using alternative cold joining techniques
- ensure clean uncoated metal
- welding in a way that produces less fume
The specific controls for the welding task depends on the following (they should be documented in your risk assessment)
- Environment and location e.g. indoors, other welding activities in workplace
- Size and shape of workpiece
Controls include:
- A well ventilated work area
- Local exhaust ventilation (LEV) which suits the work activity for example, moveable extraction arms (elephant trunks) are unlikely to be suitable for a continuous weld on a large workpieces etc. so alternative LEV Systems such as on tool extraction must be considered.
- Where exposure cannot be adequately controlled using engineering measures, then the welder must also wear appropriate respiratory protective equipment (RPE).
- When welding outdoors, local exhaust ventilation (LEV) is unlikely to be effective and RPE will be needed instead.
- Controls are required to ensure compliance with the current legal requirement for risk assessment, engineering control measures and applying the Hierarchy of Control.
There are ongoing legislative amendments and continuing research in the area of welding fume exposure. For example, low manganese welding wires are now available.
A precautionary approach is advised to control welding fume exposures to the lowest levels practicable. The work area should be well ventilated with suitable local extraction also in place and /or with Respiratory Protective Equipment provided and worn.
back to top